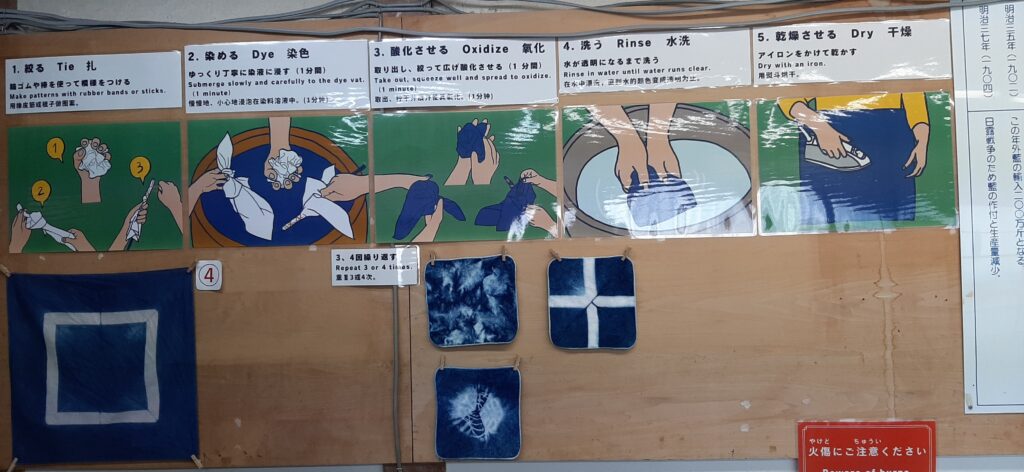
Our first visit was the Ai-no-Yakata indigo workshop. We got an instruction on the dye process and given few options of shibori technique we can try. Ingo choose shibori with rubber band, I chose to do Murakumozome, which is to hold fabric in hand..
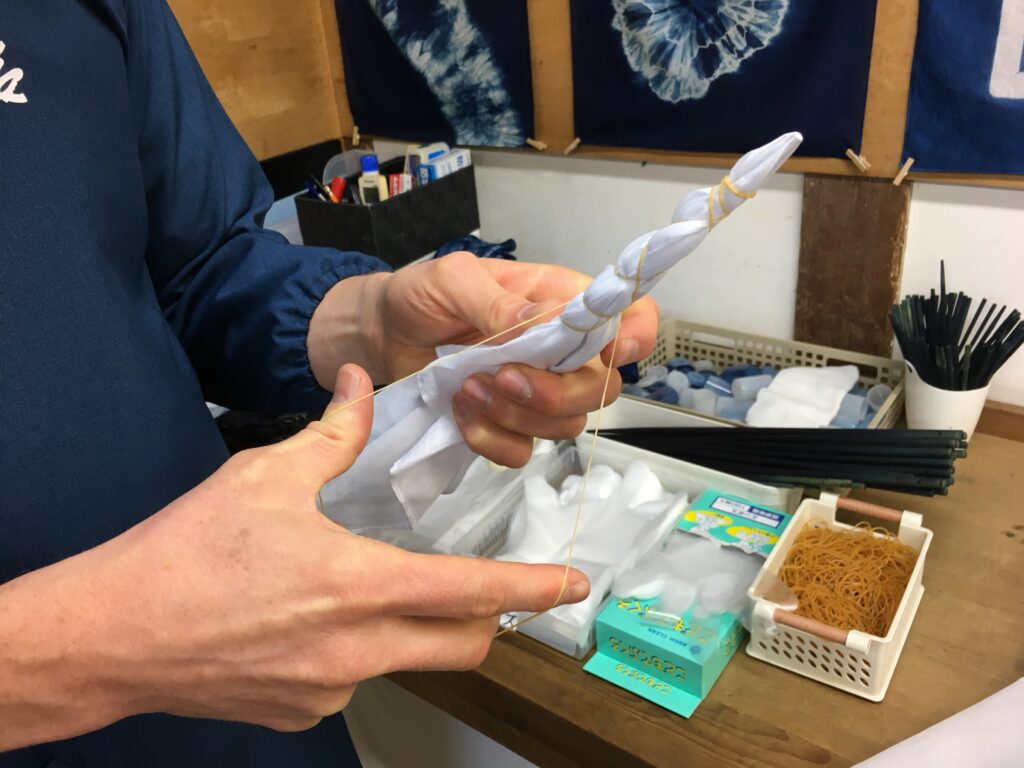
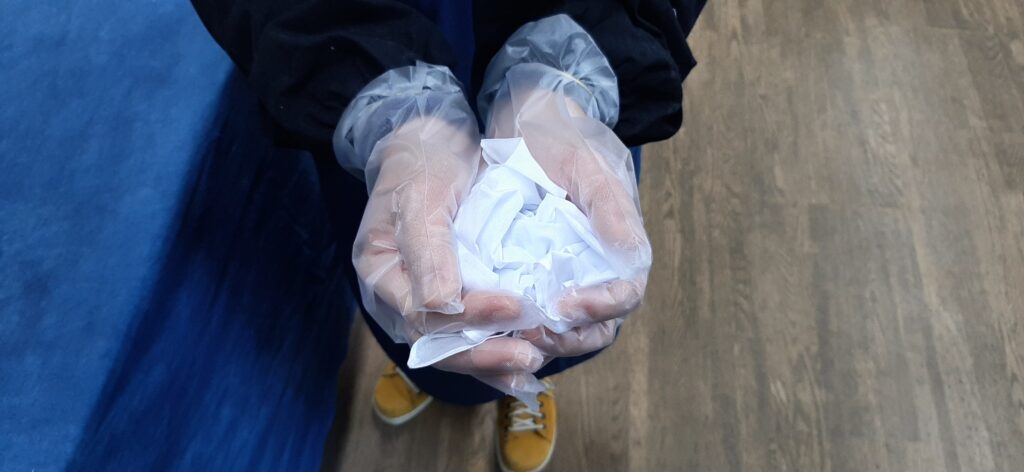
This is their dye vat/ küpe. The system has 4 vat, each of them are ceramic bases (~80cm diameter, 130cm deep) and the middle is a heating chamber. In the old system, they will put fire (burned straw) in it to keep the küpe warm on cold days. In the modern system, they have electric heating in them or around the bases.
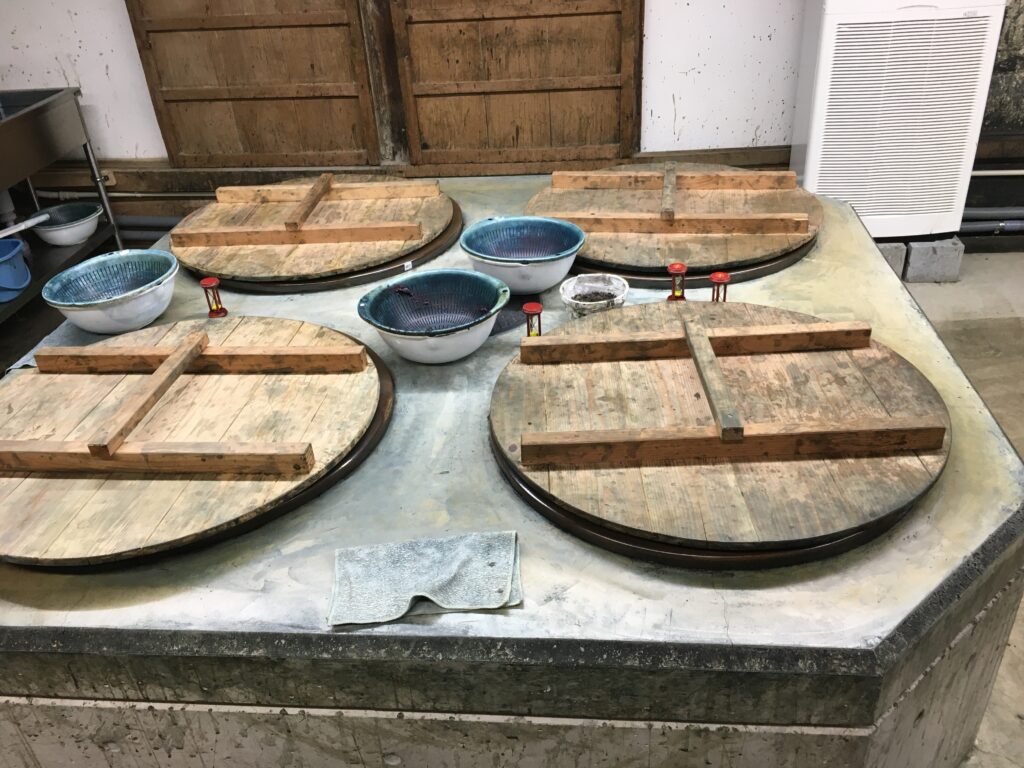
Each of these 4 küpe are in different states. Some are newly made and coloring is very strong, some are older and the colors very little. Depending on the color you want to get, and at what steps of dying you are applying, they choose different küpe to use. At Ai-no-yakata, they remove the indigo flower before the use of küpe to a side, and they put it back at the end of the day. At the end of the day around 15:00, they mix the küpe with a long bamboo stick.
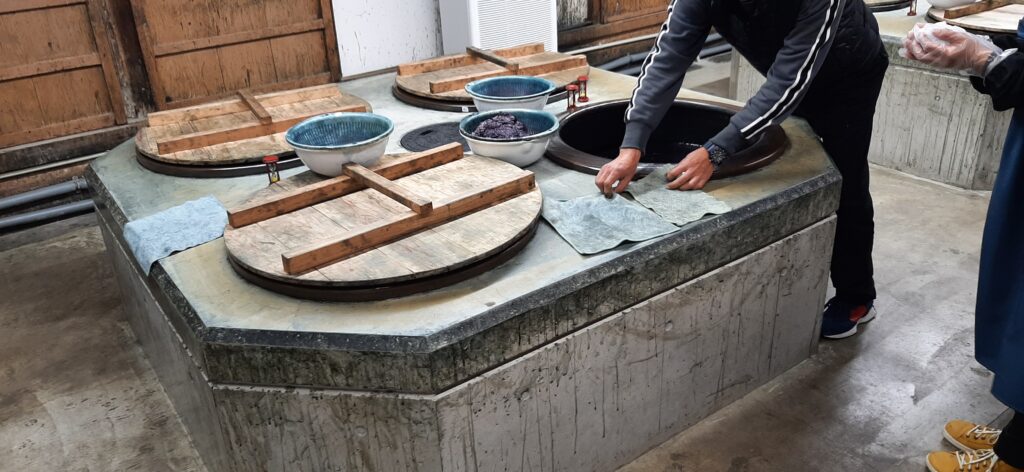
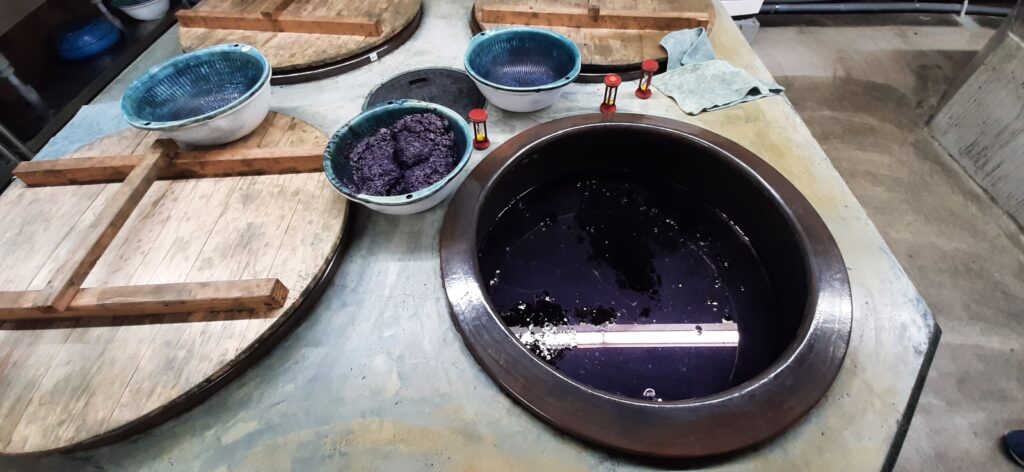
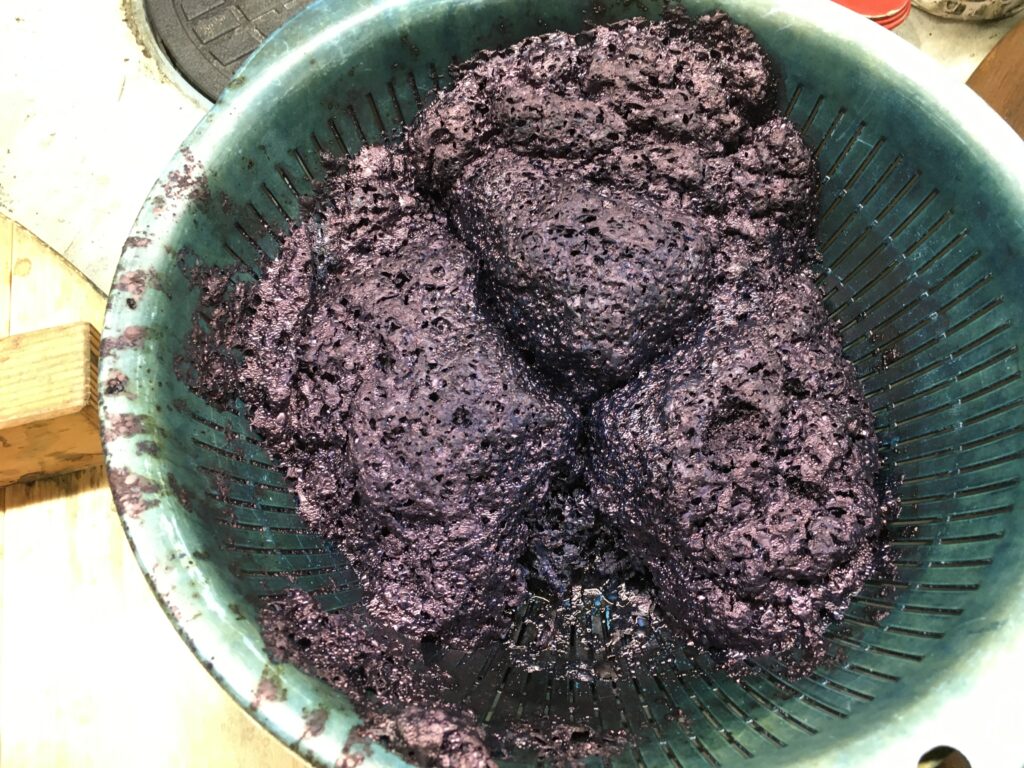
I was told to hold the fabric in my hand in the küpe, slightly shaking it for 1 min. Afterwards, take it out and let it air for 1 min. We repeated this process for 6 times. It was quite impressive that even after the first dip, it was already colored quite deep already.
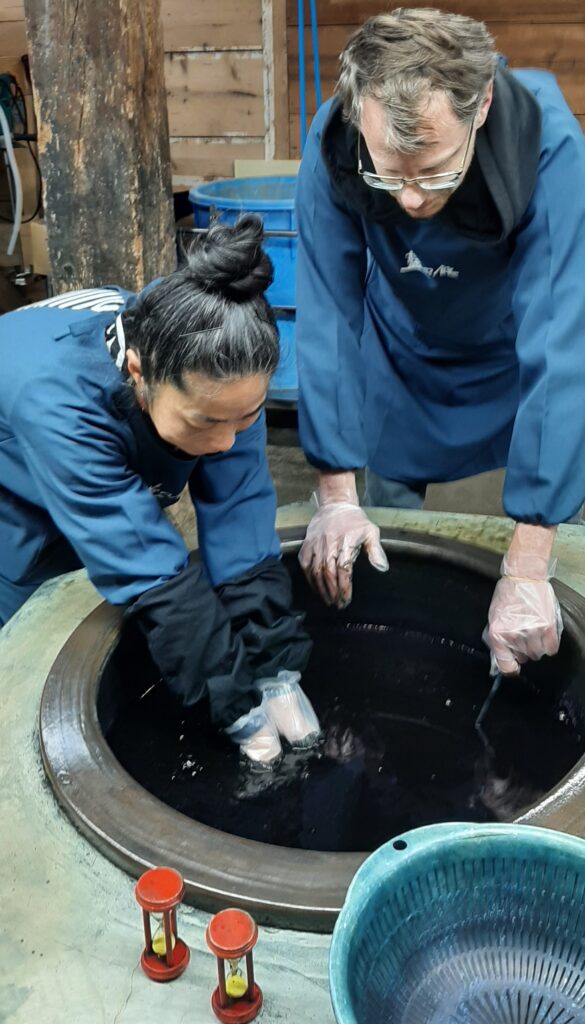
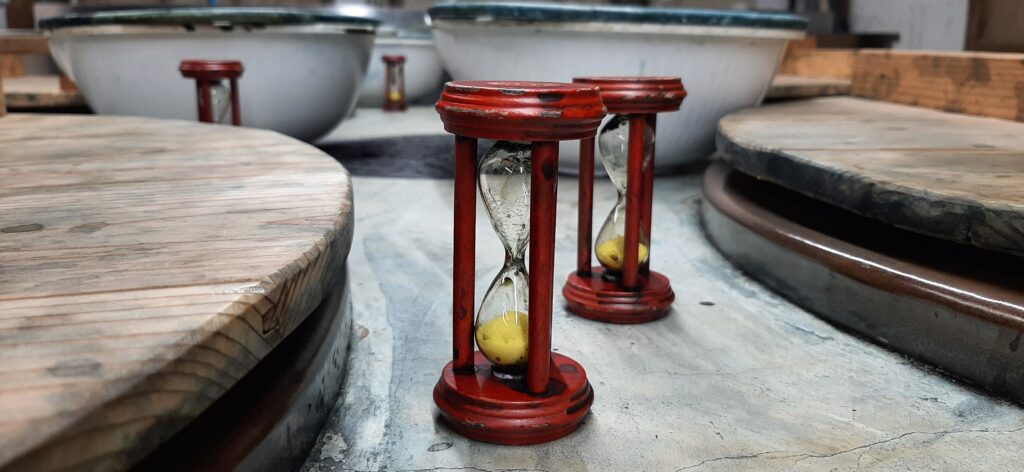
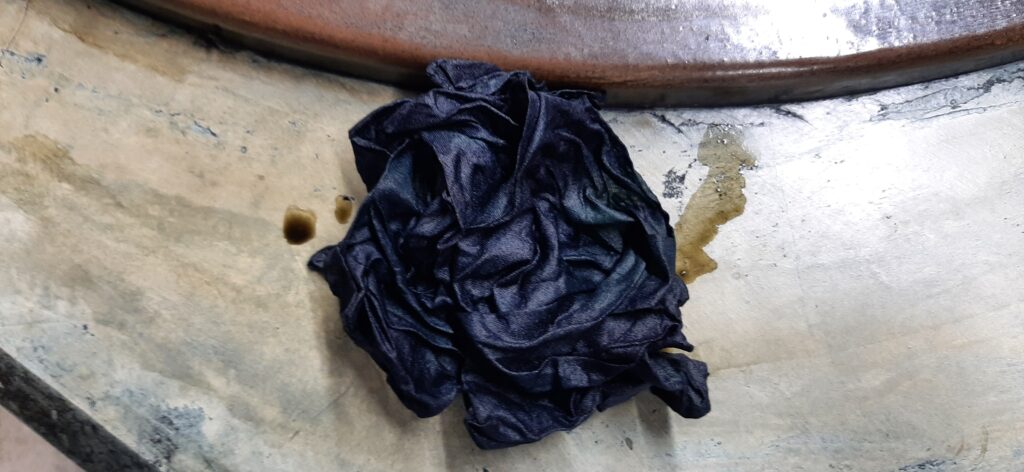
The workshop leader told ingo to open the non-tied part of the shibori when it is laying outside a bit so it gets exposed to the air. It was also important to move/massage the shibori in the küpe so the inner side of the shibori between the tied points also touches the vat water.
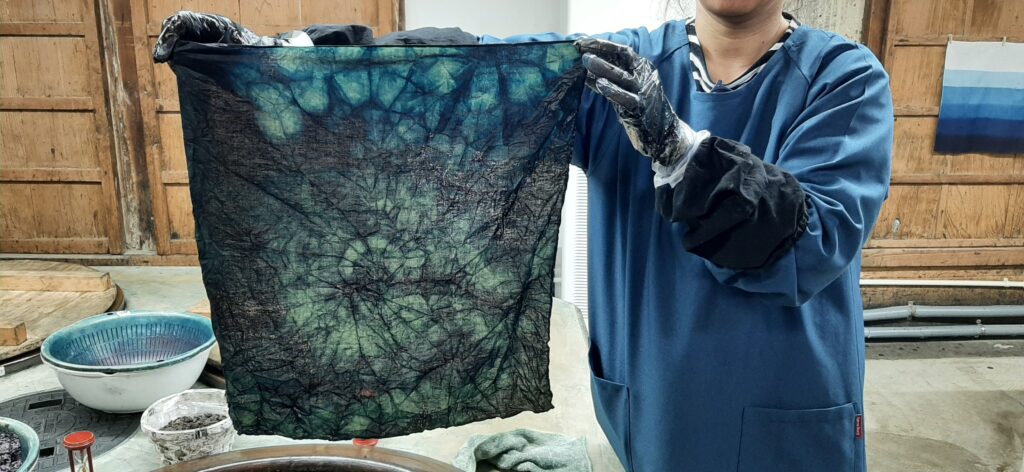
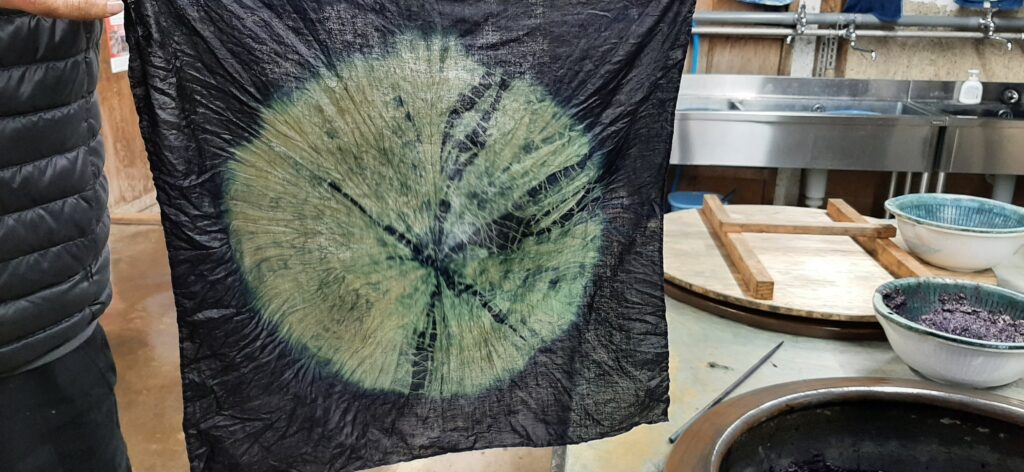
This is after 6 cycles of 1min in, 1min out. Even now it is opened up and exposed to the air, it still remains slightly green.
This is a strange thing I learned, when you expose it to water, it starts to turn blue. This is because the indican on the fabric is oxidizing with water and becoming indigotin, which is the blue color of the indigo. In all the sukumo dying places I went, they talked about this second step of oxidation in water when washing.
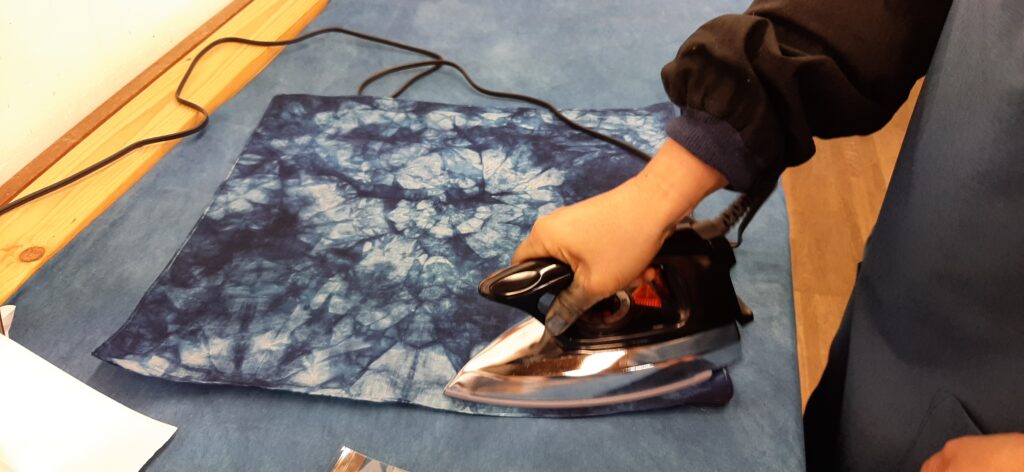
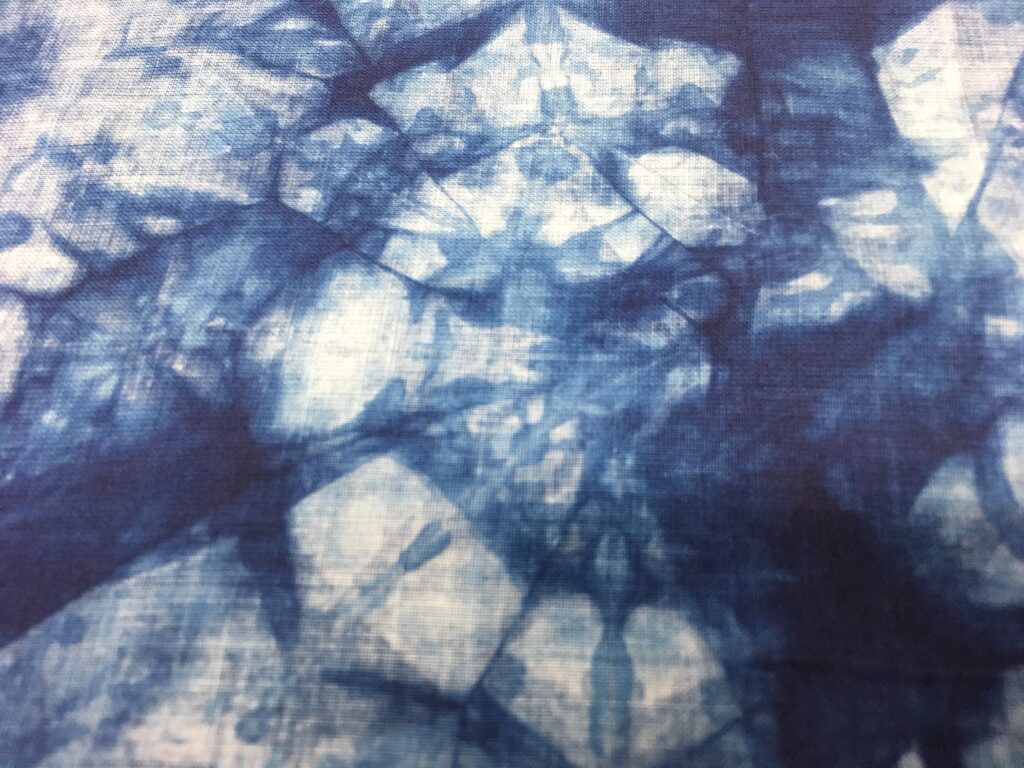
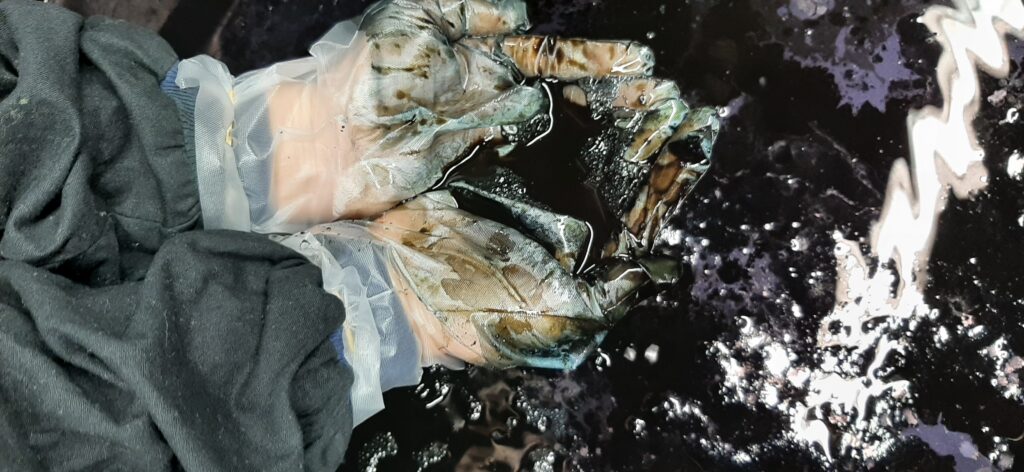
This is the color of the küpe. I was surprised how brown and dark it is. It is different from the yellow green liquid I am used to at the Zeugfärberei. Their küpe is pH10.5, kept around 28 degrees. They sometimes use pH meter to measure the pH, but often they feel the liquid with bare hand and see how “slimy” it feels on skin to tell roughly how high the pH is. Another way is to taste the küpe. As it is alkali, it tastes bitter and gives a bit of tingling sensation on the tongue. When pH is too low, they add potash (K2CO3) or lime stone to the küpe, when it is too high, they just let it be or dye some fabric and let the pH naturally drop to the ideal range.
As pH is not extremely high, the dyers working there are not wearing gloves. My plastic glove accidently had a hole and my thumb gut blue. The blue color on my skin came out after washing few times, but my nail remained blue for a week.
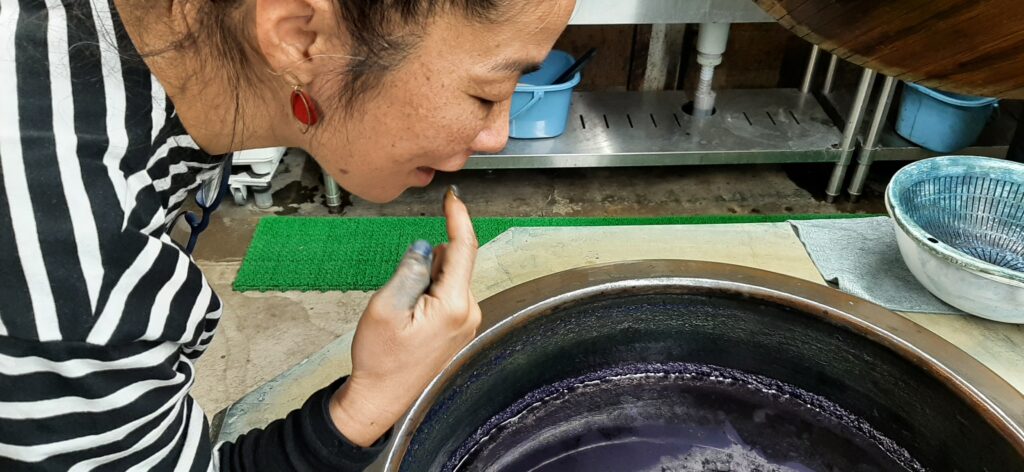
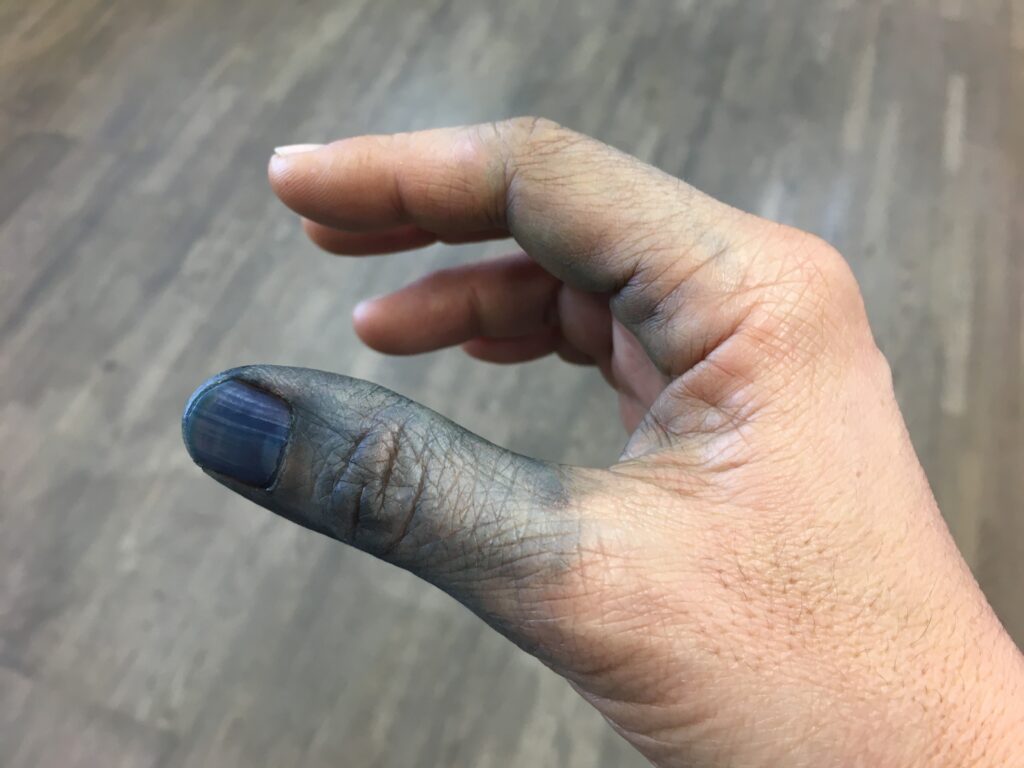
This is how the dyers were dying small shibori pieces in the küpe. Hang a big sheave and let the shibori pieces swim in the küpe so that the pieces does not fall into the küpe but one does not get a marking from hanging. Often they shake the fabric, let the folded part open a bit inside so they get dyed evenly.
The last photo is the küpe that is almost finished. At this state, it does not dye fabric anymore and they need to remake the küpe. They said their küpe lasts 3-6 months depending on how much they dye in it. The leftover of the küpe can be spread into the farming field as fertilizer.
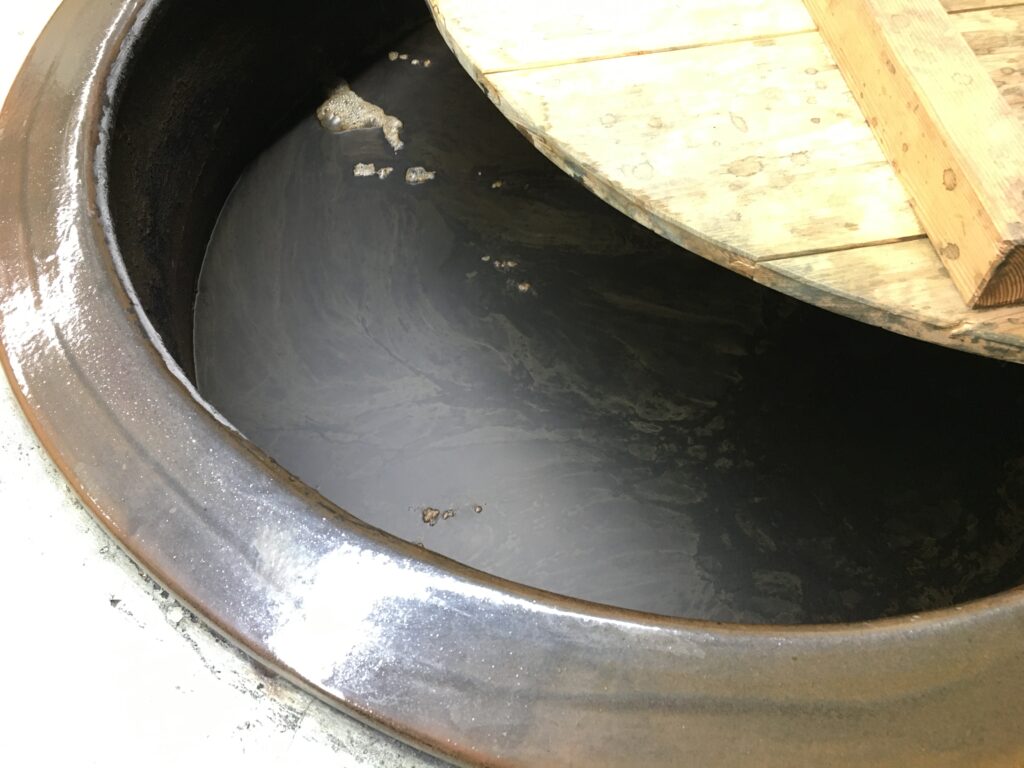
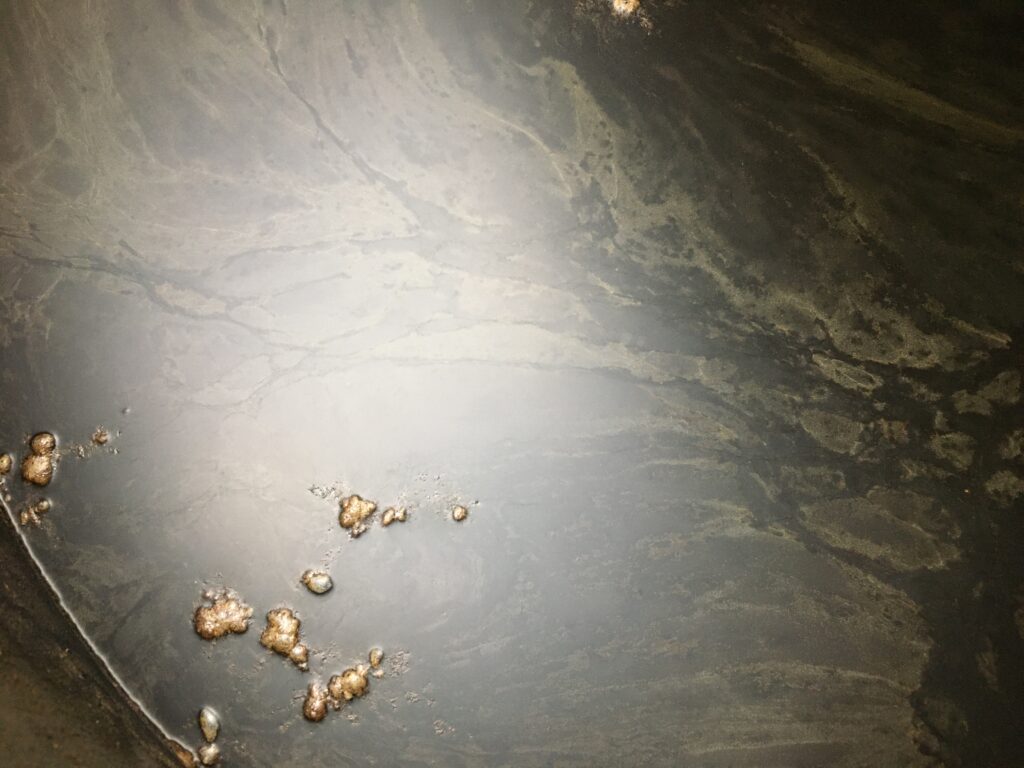