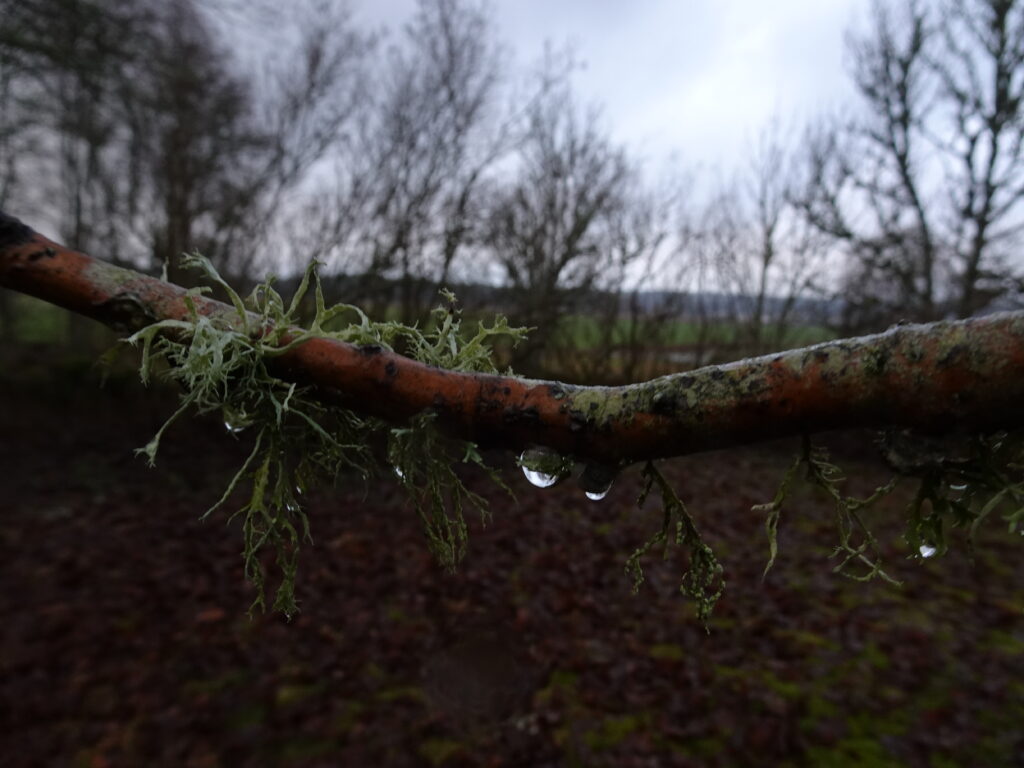
Today starts with rain. Mag has a nice idea to go for field recording of the sound of rain. While she captures sound with her zoom recorder, I try to make some short video clips of different rain scenes.
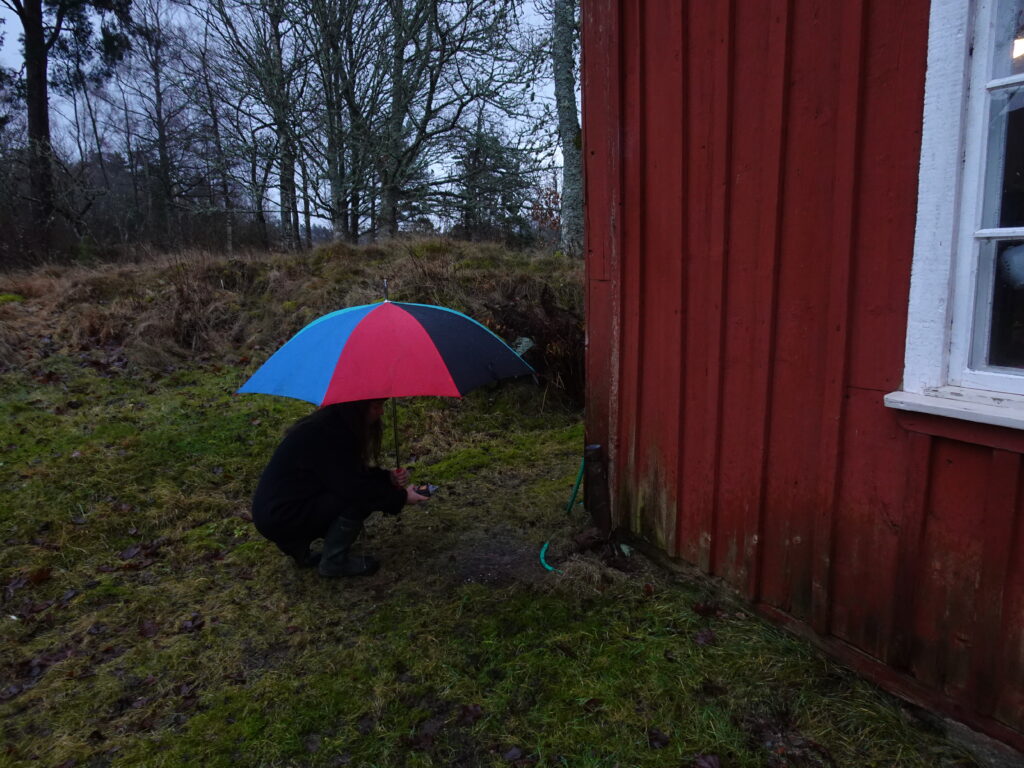
Back inside, I start off the day with checking the bend sensors. These kinesiology tape sensors are quick to make, and great to stick on the body as you want to place them… but it seems to get flattened and the reading range changes over time. I read each of them with the multimeter. All of them started off by ranging somewhere 200k ohm to 50k ohm, now some are measuring 80k ohm when not touched, and goes down around 30k ohm.
At the moment I am using 100k ohm pull up resisters to create voltage divider circuit to read them on analog ports. I will need to change the resister to smaller size, something like 47k ohm. I check my resister box, and of course I am missing 47k. I only have 2 more left in the box. Bad preparation. I decide to substitute some of them with 27k ohm instead.
I have modified Bela board a bit to use in this project. Cut-up breadboard is stuck in the middle of the Bela, so you can quickly prototype a circuit with jumper cables. I have also added a big capacitor (I think this one is 2000uF). This is to avoid power failure. As it is worn on body, it can pull the battery plug sometimes and cause a short power failure (it happened in another project). The capacitor provides a backup power in case battery power connection fails. Now I changed some of the resistors on the breadboard to 47k/27k ohm.
The Bela board sits on a collar. It has 2 power mesh (very stretchy mesh) pocket: one holds power bank battery, and the other holds Bela. I used paracord to create isolated conductive thread cables. Paracord has inner core that you can pull out and insert conductive thread instead. I have added 90degree angle header on one side to connect with the breadbaord, and coated with black hot glue (did not have to be black.. just what I had in the studio). The other end of the cable is connected with a conductive fabric and pressed with 7mm poppers to allow further connections with fabric/ sensors.
The color also has 4 LEDs. it is a normal SMD LED connected with conductive thread (I should have taken picture!) then covered with semi-transparent beads so you do not scratch it off by mistake, and also to defuse the light. Bela mini does not have analog out pins.. so I am using digital out and making my own PWM on PureData… which makes it a bit flicker-ly… We use these LEDs to see what are the control values coming out from the sensor reading, if it is sending anything at all, when the “next sample” signal is sent… so on. It is helpful to have some kind of display for the development process.
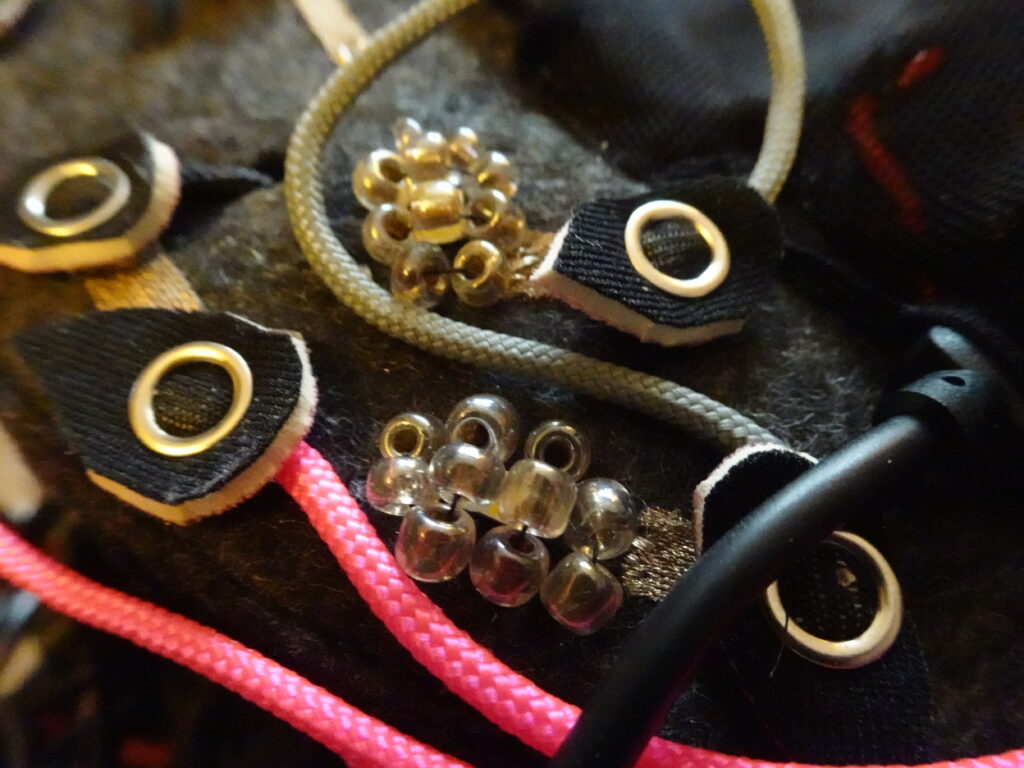
Today, we are testing the setting with a glove on Mag’s left hand, and 2 wrist sensors, 1 elbow sensor. The idea is to use some hand gestures for control/mode change together with wrist sensor for knob controls. I am connecting 3 of the finger bend sensor on the glove to Bela.
The glove’s 3 sensors readings are fed into svm (support vector machines) object to detect hand gestures. We trained 3 gestures, open hand (nothing), closed hand (gesture1) and thumb/index finger closed (gesture2). In the DJ patch, gesture1 triggers to pick next sound sample files, and gestrue2 switches the mode of 1 play head to 2 play heads. After some tweaking, it seems to work well. We skip the elbow sensor and stick with the glove and the wrist sensors.
Mag has to control a lot of instruments while she plays. The sensors we put on so far is not interfering with other play. She has to concentrate when she uses the sensors as it is getting more and more complicated… she said she needs to practice it.